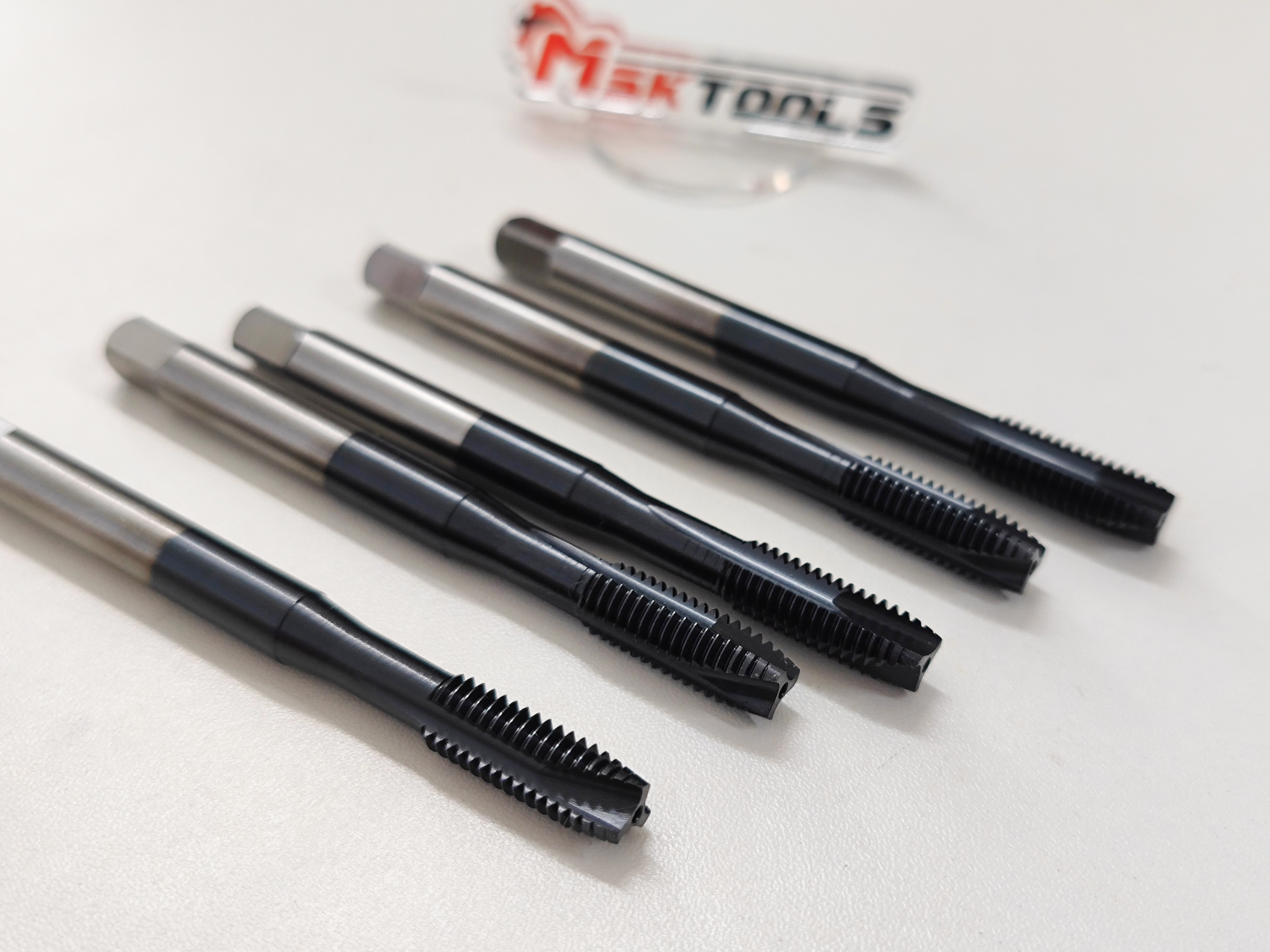

Part 1

The coating is applied through a process known as physical vapor deposition (PVD), which results in a hard, wear-resistant layer that significantly improves the performance and durability of the coated tool. TICN-coated taps offer several advantages that make them highly preferred in the industry.First and foremost, the TICN coating provides exceptional hardness and wear resistance to the tap, allowing it to withstand the high temperatures and abrasive forces encountered during the cutting process. This translates to extended tool life and reduced frequency of tool replacements, ultimately leading to cost savings for manufacturers.
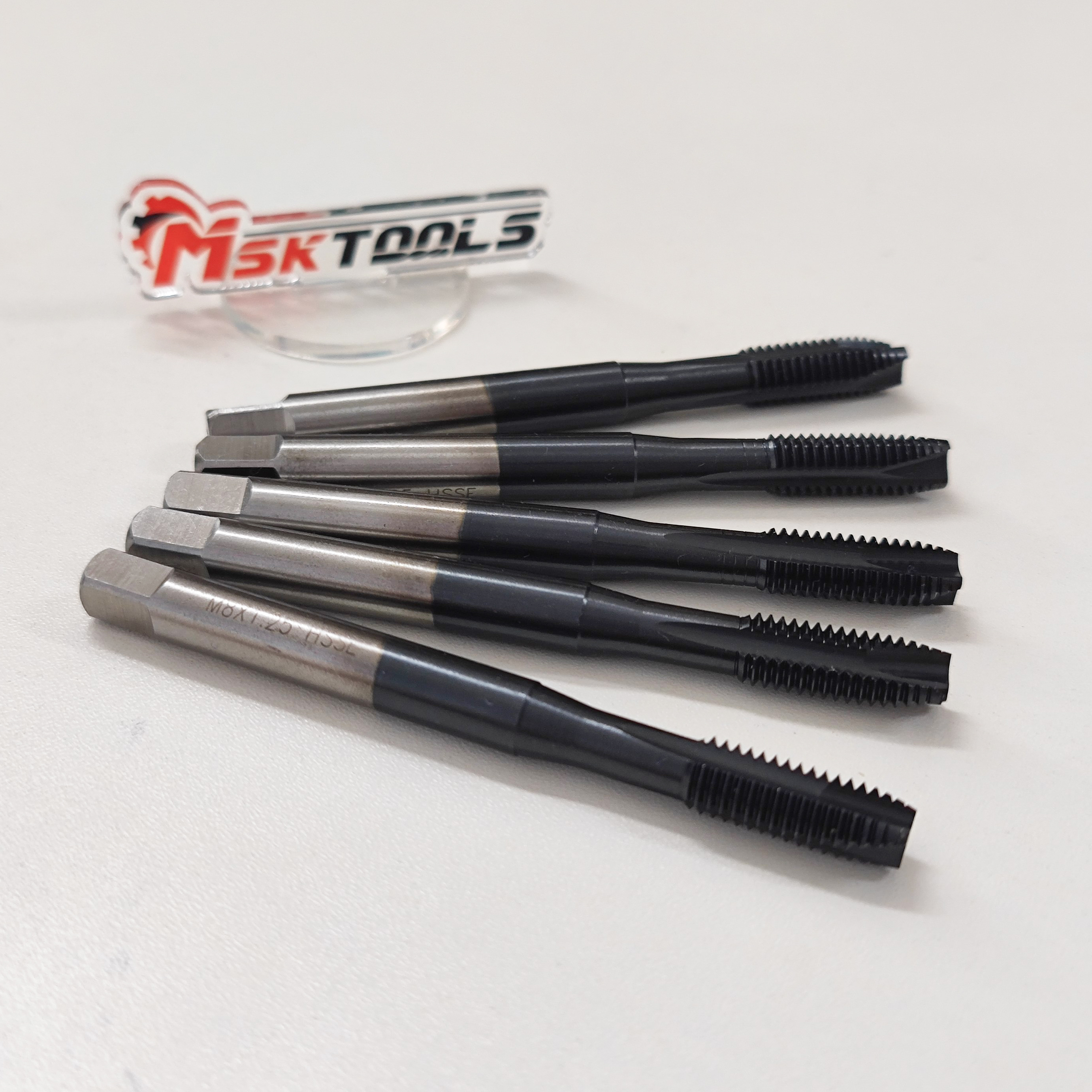

Part 2

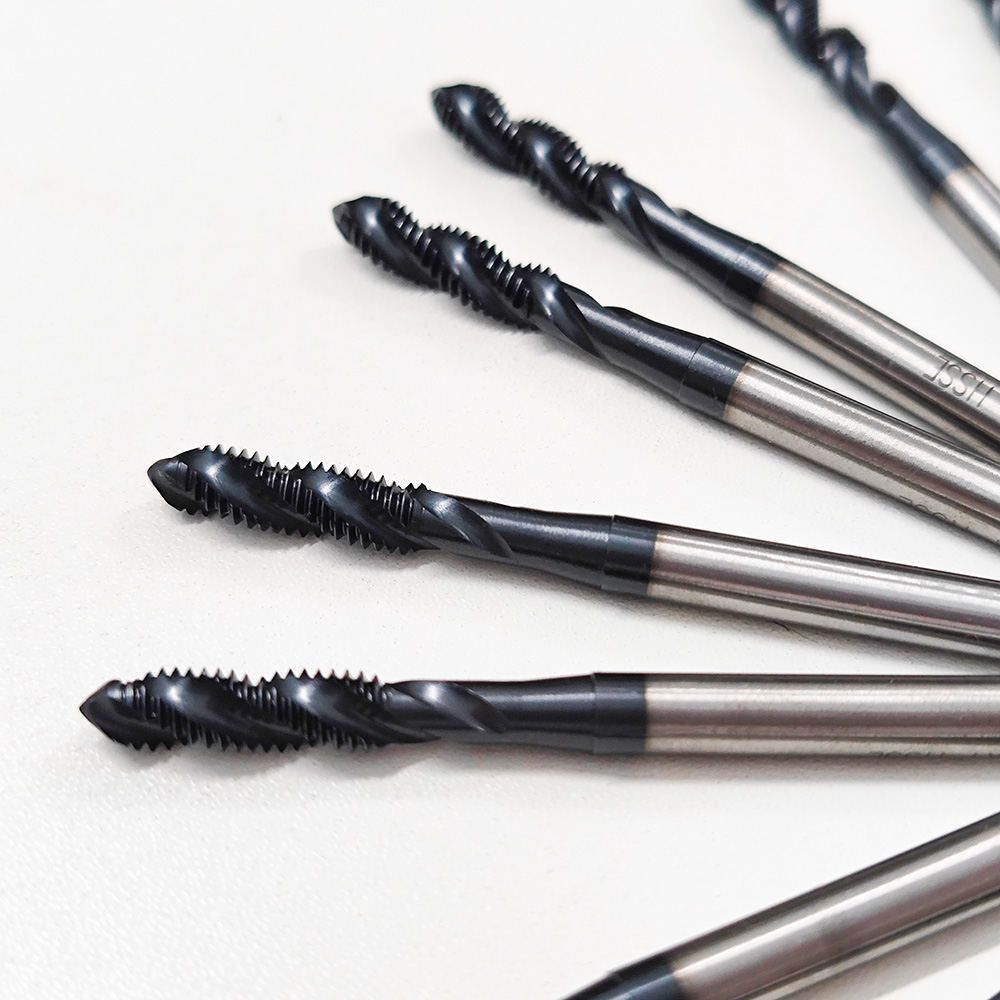
Additionally, the increased wear resistance of TICN-coated taps contributes to improved thread quality and dimensional accuracy, ensuring that the threads produced meet the required specifications.Moreover, TICN coating reduces friction during the tapping process, resulting in smoother chip evacuation and lower torque requirements. This characteristic is particularly beneficial when threading harder materials or alloys, as it minimizes the risk of tool breakage and reduces the power consumption during machining.

Part 3

The reduced friction also leads to cooler cutting temperatures, which can help prevent workpiece and tool overheating, thereby contributing to improved machining stability and surface finish.Furthermore, TICN-coated taps exhibit enhanced chemical and thermal stability, making them suitable for a wide range of cutting applications, including high-speed machining and demanding production environments. The corrosion resistance of the coating protects the tap from chemical reactions with the workpiece material and cutting fluids, preserving the tool integrity and performance over extended periods of use.In terms of applications, TICN-coated taps are widely employed in industries such as automotive, aerospace, precision engineering, and mold and die making, where high-performance threading solutions are imperative.
The use of TICN-coated taps has proven beneficial in producing threads in materials such as stainless steel, titanium, hardened steel, and cast iron, where the combination of hardness, wear resistance, and thermal stability is critical for achieving consistent and reliable results.In conclusion, TICN-coated taps represent a significant advancement in the field of thread cutting tools, offering unparalleled performance, durability, and versatility in various machining applications. The adoption of TICN coating technology has redefined the standards for thread cutting efficiency and quality, empowering manufacturers to optimize their production processes and achieve superior thread accuracy and integrity. As the demands for precision and productivity continue to evolve, TICN-coated taps stand as a reliable solution for meeting the challenges of modern manufacturing.
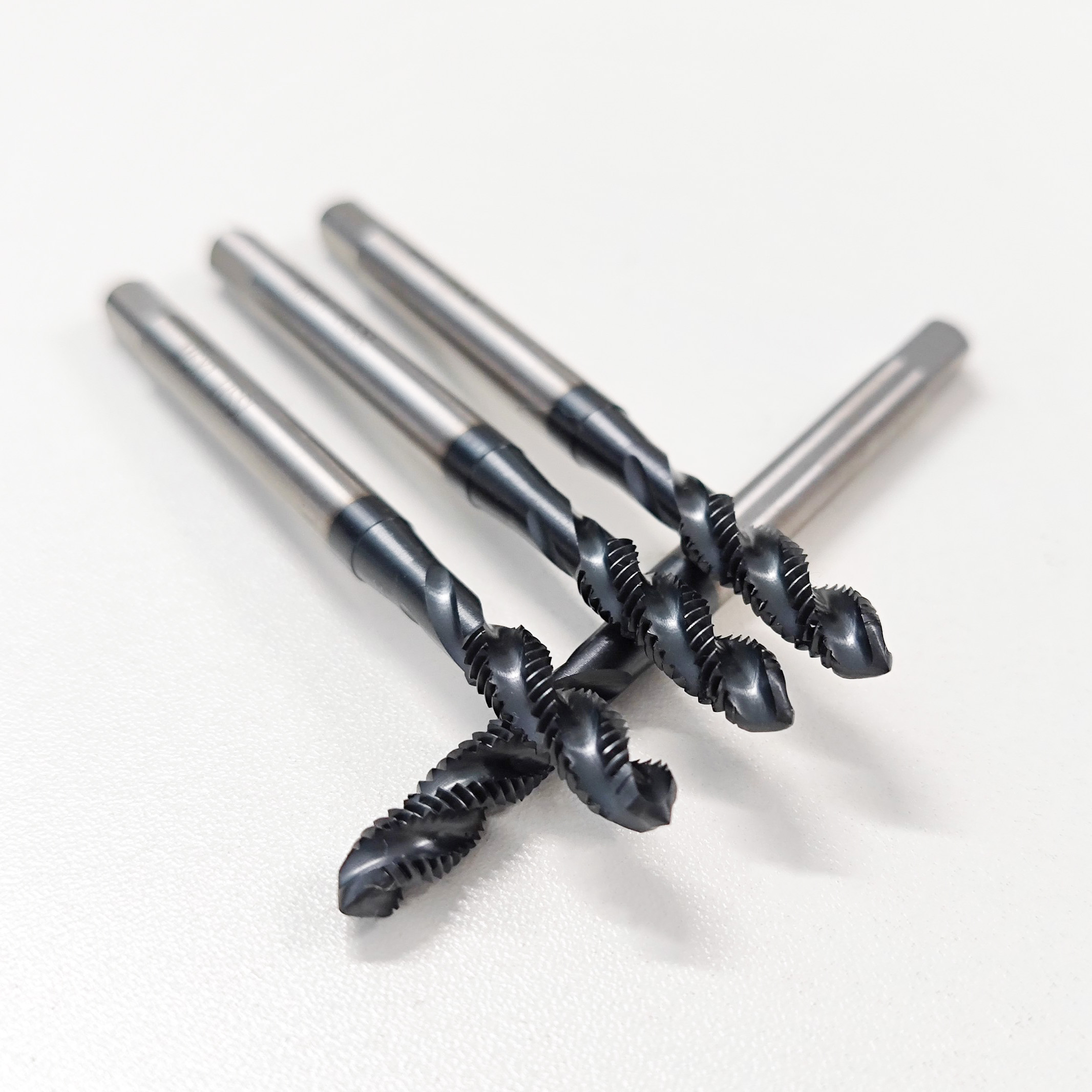
In summary, the utilization of TICN-coated taps has become increasingly prevalent in the manufacturing industry, driven by the need for superior threading solutions that deliver extended tool life, enhanced performance, and consistent thread quality. The application of TICN coating technology represents a significant advancement in the field of cutting tools, facilitating improved efficiency and cost-effectiveness in thread cutting operations.
With their exceptional hardness, wear resistance, and thermal stability, TICN-coated taps have established themselves as indispensable tools for achieving precision threads in a wide range of materials and applications. As the industry continues to prioritize quality, productivity, and sustainability, the adoption of TICN-coated taps is poised to remain a key strategy for meeting the evolving demands of modern manufacturing.
Post time: Feb-29-2024