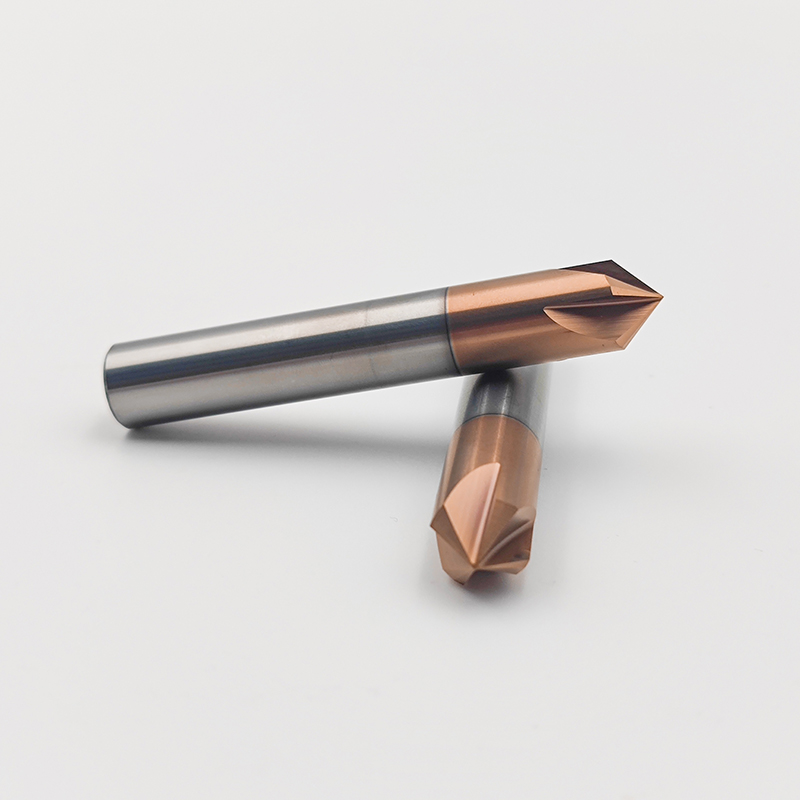

Part 1

In the world of CNC machining, efficiency and precision are key factors in achieving high-quality results. One crucial aspect of this process is the use of spot drills, especially when working with materials of varying hardness such as HRC45 and HRC55. In this blog, we will explore the importance of using high-quality carbide spot drills, specifically those from the renowned MSK Brand, to optimize CNC machining operations for these challenging materials.
Understanding the Challenge: HRC45 and HRC55 Materials
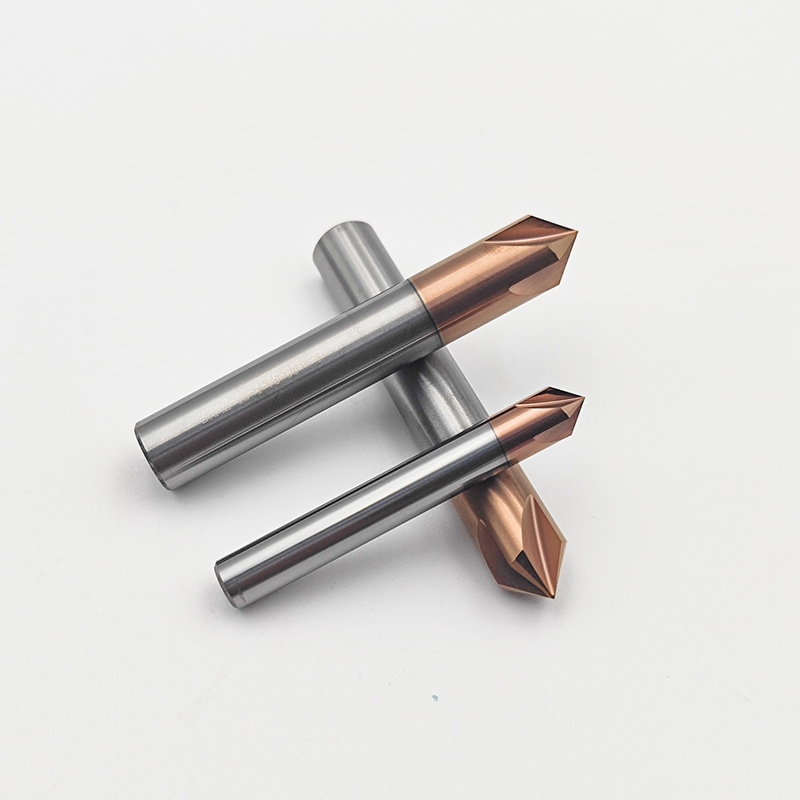
Before delving into the specifics of spot drills and their role in CNC machining, it's essential to understand the unique challenges posed by materials with hardness levels of HRC45 and HRC55. These materials, often used in industries such as aerospace, automotive, and tooling, require precision machining techniques to achieve the desired results.
HRC45 and HRC55 materials are known for their toughness and resistance to wear, making them ideal for applications where durability and strength are paramount. However, these same properties also make them more difficult to machine, requiring specialized tools and techniques to achieve precise cuts and drilling operations.

Part 2

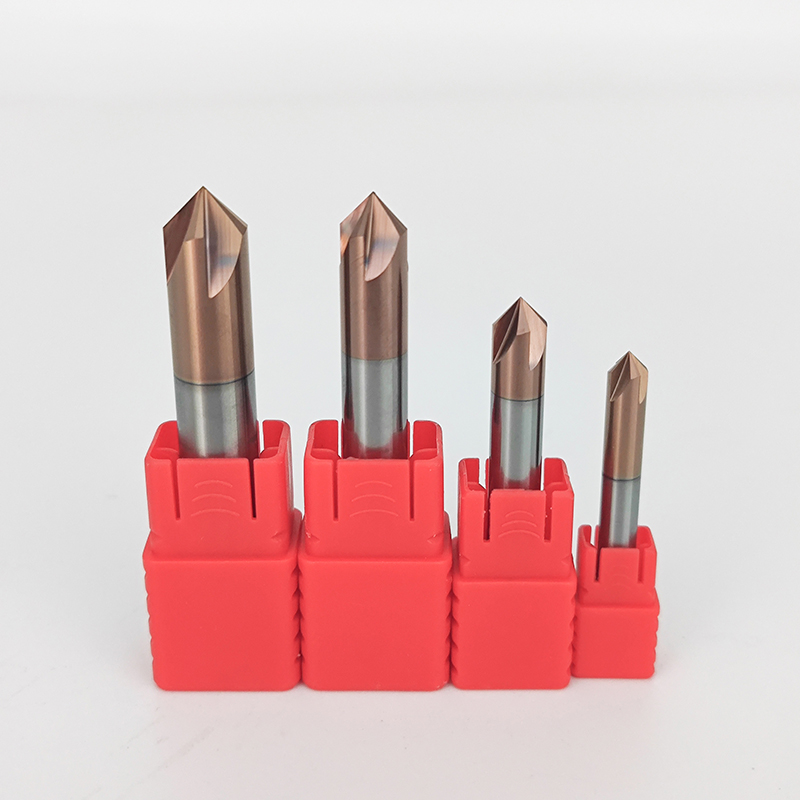
The Role of Spot Drills in CNC Machining
Spot drills play a crucial role in the CNC machining process, particularly when working with hard materials like HRC45 and HRC55. These tools are designed to create a starting point for drilling operations, providing a precise location for subsequent drilling or milling processes. By creating a small, shallow hole at the desired location, spot drills help ensure accuracy and consistency in the machining process.
When it comes to working with challenging materials, the quality of the spot drill becomes even more critical. Inferior spot drills may struggle to penetrate the surface of HRC45 and HRC55 materials, leading to imprecise drilling and potential tool wear. This is where high-quality carbide spot drills, such as those offered by MSK Brand, come into play.
The MSK Brand Advantage: High-Quality Carbide Spot Drills
MSK Brand has established itself as a leading manufacturer of cutting tools, including carbide spot drills renowned for their exceptional performance in CNC machining applications. These spot drills are specifically designed to meet the demands of hard materials, offering superior durability, precision, and efficiency.
One of the key advantages of MSK Brand carbide spot drills is their composition. Made from high-quality carbide materials, these spot drills are engineered to withstand the rigors of machining HRC45 and HRC55 materials. The hardness and toughness of the carbide ensure that the spot drills maintain their cutting edges and performance over extended periods of use, resulting in consistent and reliable machining outcomes.
Furthermore, MSK Brand spot drills are designed with optimized geometries and coatings to enhance their cutting capabilities. The geometry of the drills is tailored to provide efficient chip evacuation and reduced cutting forces, minimizing the risk of tool deflection and breakage when working with hard materials. Additionally, advanced coatings such as TiAlN and TiSiN further enhance the wear resistance and heat dissipation properties of the spot drills, prolonging their tool life and maintaining cutting edge sharpness.

Part 3

Maximizing Efficiency and Precision
By incorporating MSK Brand carbide spot drills into CNC machining operations for HRC45 and HRC55 materials, manufacturers can maximize efficiency and precision while minimizing tool wear and downtime. The superior performance of these spot drills allows for faster and more accurate drilling operations, ultimately leading to higher productivity and cost savings.
In addition to their performance benefits, MSK Brand spot drills also contribute to the overall quality of machined parts. The precise starting points created by these spot drills ensure that subsequent drilling and milling processes are carried out with accuracy, resulting in finished components that meet stringent dimensional and surface finish requirements.
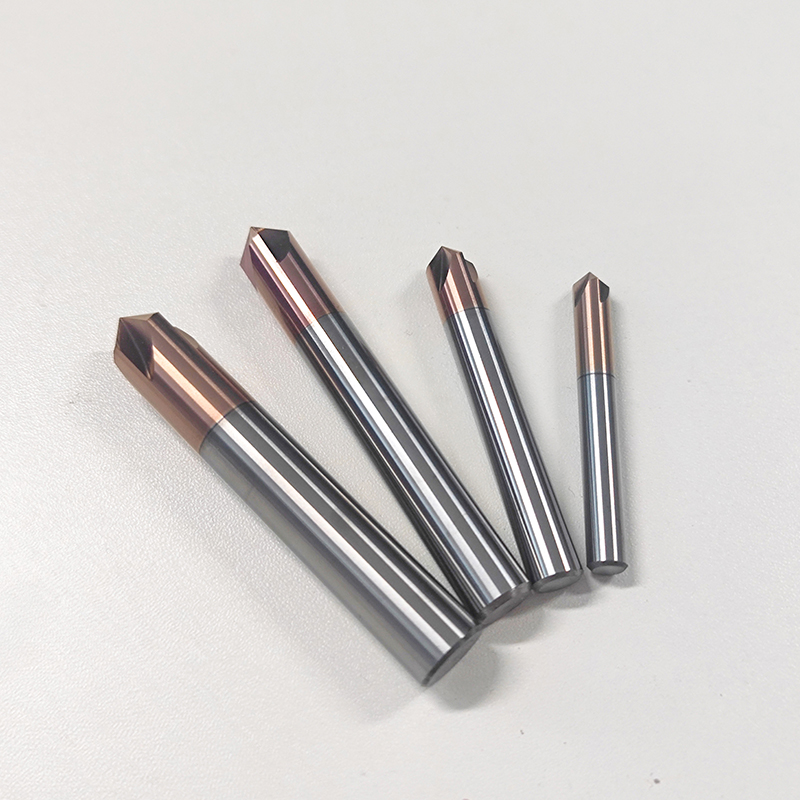
Ultimately, the use of high-quality carbide spot drills from MSK Brand empowers CNC machinists to tackle the challenges posed by HRC45 and HRC55 materials with confidence, knowing that they have the right tools for the job.
Conclusion
In the world of CNC machining, the choice of cutting tools can make a significant difference in the efficiency and quality of the machining process. When working with hard materials such as HRC45 and HRC55, the use of high-quality carbide spot drills, such as those offered by MSK Brand, is essential for achieving optimal results.
By leveraging the superior durability, precision, and performance of MSK Brand spot drills, manufacturers can enhance their CNC machining operations, leading to increased productivity, reduced tool wear, and superior part quality. As the demand for precision-machined components continues to grow, investing in high-quality cutting tools like MSK Brand carbide spot drills becomes a strategic decision for staying ahead in the competitive manufacturing landscape.
Post time: Mar-27-2024