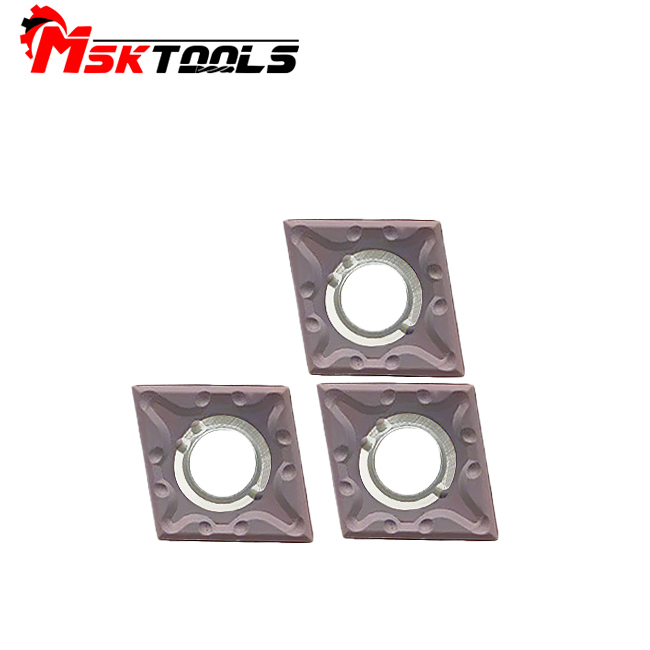
CNC Turning: Unlocking the Potential of Carbide and Carbide Inserts with External Turning Tools
In the field of precision machining, CNC lathe turning is a proven method that has revolutionized manufacturing. The technology has become an indispensable tool for many businesses due to its ability to produce complex parts with high precision. When it comes to maximizing the efficiency and performance of CNC lathe turning, one cannot overlook the importance of carbide and carbide inserts, especially when paired with the correct external turning tool.
Carbide is a combination of carbon and metal, highly regarded for its exceptional hardness and wear resistance. When carbide inserts are employed, it becomes the first choice for machining operations requiring durability and longevity. Tungsten carbide inserts, in particular, are highly valued for their superior strength and ability to withstand high cutting forces. These inserts are designed to fit precisely into the tool holders of CNC lathes for safe and efficient machining operations.
An important aspect to consider when using carbide or carbide inserts is the selection of external turning tools. External turning tools are usually solid or indexable inserts that make contact with the workpiece and remove material to shape it to the required specifications. By combining the right external turning tools with carbide or carbide inserts, manufacturers can take full advantage of the advantages these materials have to offer.
The first step to achieving the best results is selecting an external turning tool that complements the characteristics of the carbide or tungsten carbide insert. It should have a strong and rigid structure to withstand cutting forces, and sharp cutting edges to ensure clean and precise cuts. Additionally, careful consideration should be given to tool geometry and chipbreaker design to facilitate chip evacuation and prevent built-up edge, which can adversely affect surface finish.
Additionally, the correct selection of cutting parameters such as cutting speed and feed rate is critical when using carbide or carbide inserts on external turning tools. Taking into account the workpiece material, hardness and desired surface finish, manufacturers can optimize their machining processes to achieve the best results. By utilizing the hardness and wear resistance of carbide inserts and the strength of carbide inserts, businesses can increase productivity and reduce tooling costs in the long run.
All in all, CNC lathe turning combined with carbide and carbide inserts has been a game changer for the manufacturing industry. When paired with the right external turning tools, these materials unlock the full potential of precision machining. By carefully selecting the right external turning tool and optimizing cutting parameters, businesses can achieve efficient and cost-effective machining operations. So whether you're a production manager or a CNC machinist, harnessing the power of carbide and carbide inserts as well as external turning tools is a surefire way to stay ahead in the ever-evolving manufacturing industry.
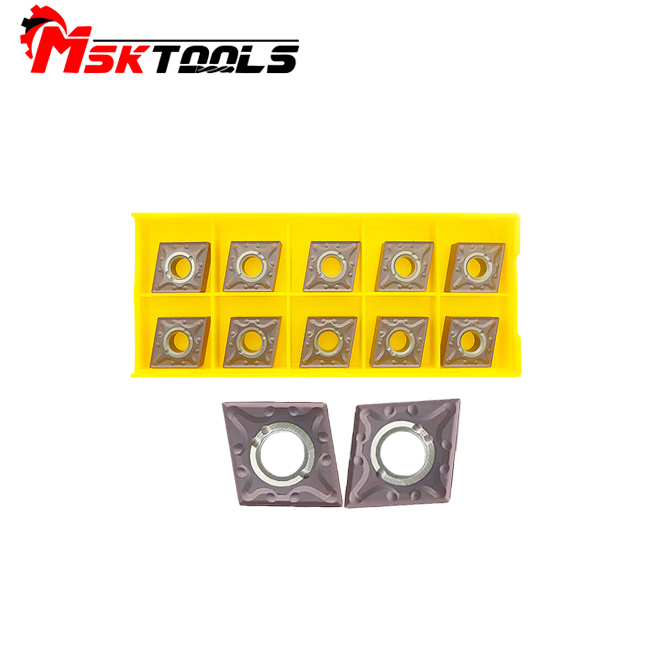
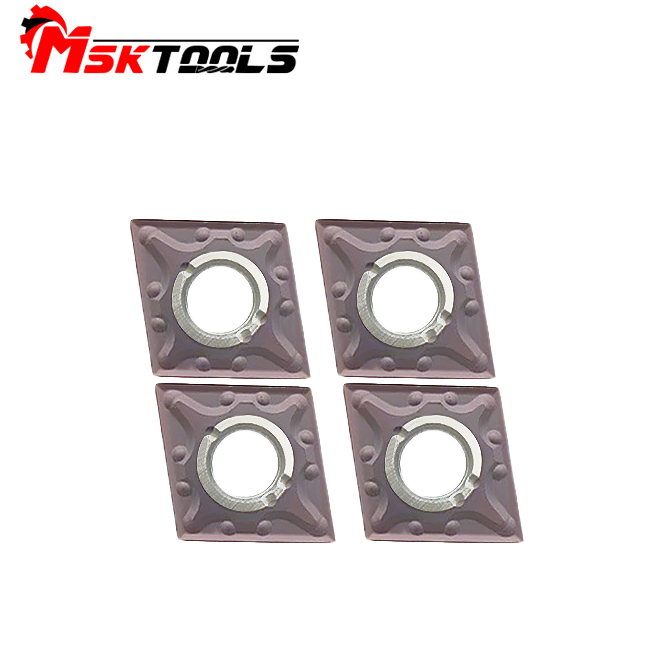
Post time: Sep-08-2023