
Part 1

In the field of precision machining, the chuck is a basic workpiece holding device that plays a key role in holding cutting tools and workpieces accurately and reliably. Chucks are widely used in a variety of machining operations, including milling, turning, grinding, and drilling, and they are known for their strong concentric clamping capabilities of the tool and workpiece. In this article, we’ll take a closer look at the importance of collets in precision machining, their different types, applications, and factors to consider when choosing the right collet for a specific machining task.
The importance of chuck in precision machining
The chuck is the critical connection between the cutting tool and the machine tool spindle, ensuring that the tool is securely held in place and accurately positioned during machining. The primary function of a chuck is to clamp the tool or workpiece with high concentricity, minimizing runout and ensuring precise machining operations. This is especially important in applications where tight tolerances and high surface finish requirements are critical.
One of the main advantages of chucks is their versatility. They can accommodate a variety of tool diameters, making them suitable for a variety of machining tasks without the need for specialized tool holders. Additionally, the chuck provides strong clamping force, which is critical to maintaining tool stability and preventing tool slippage during heavy cutting operations.

Part 2

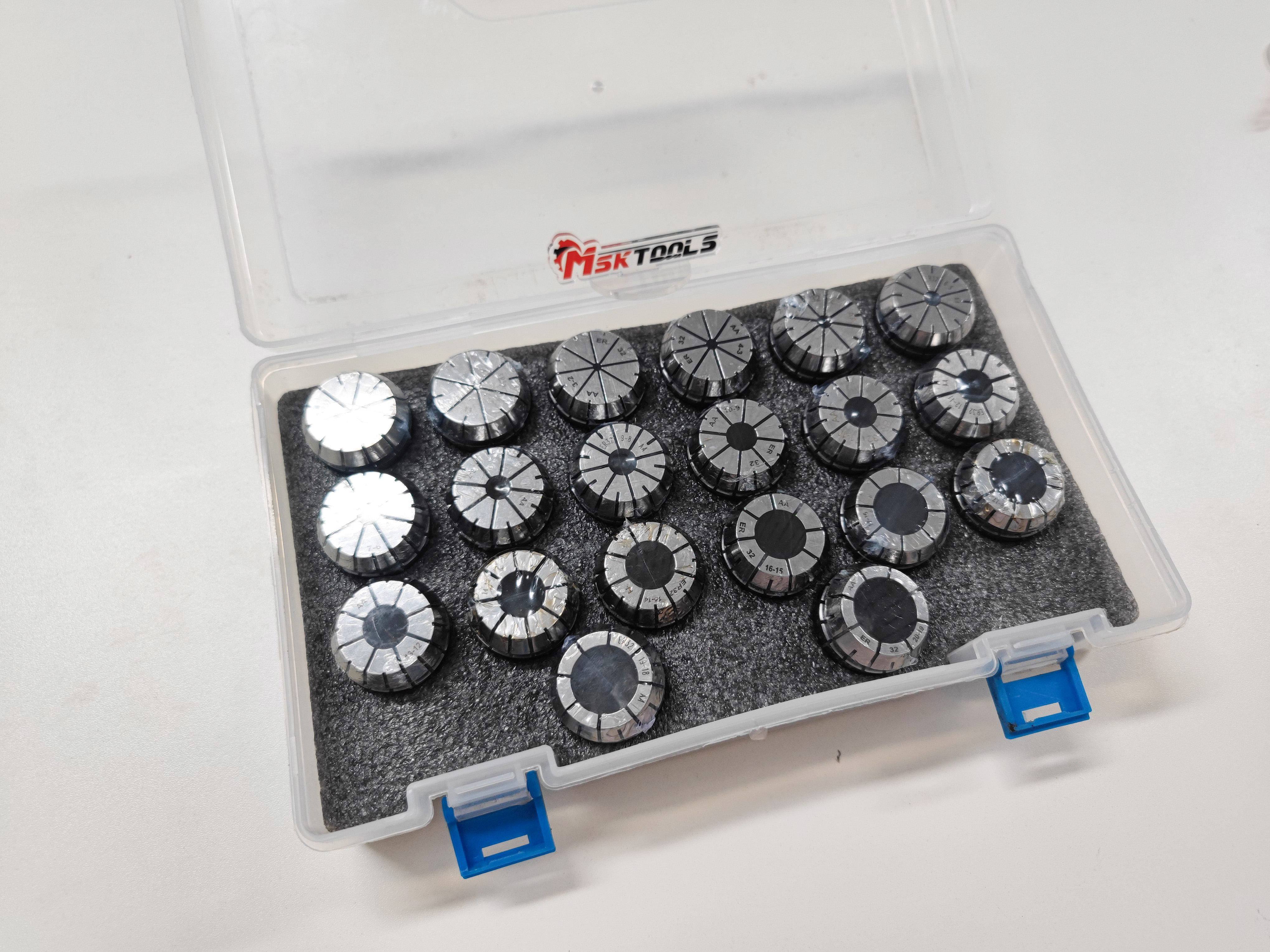
Chuck type
There are many types and configurations of chucks, each designed to meet specific machining requirements and accommodate different tool and workpiece geometries. Some of the most common collet types include:
1. Spring collet: Also known as ER chuck, it is widely used in milling, drilling and tapping operations. They feature a flexible, spring-loaded design that can expand and contract to hold tools of various diameters. ER chucks are known for their high clamping force and excellent concentricity, making them suitable for a variety of machining applications.
2. R8 chucks: These chucks are specially designed for milling machines with R8 spindles. They are commonly used to hold end mills, drills, and other cutting tools in place during milling operations. The R8 chuck provides a secure grip and is easy to replace, making it popular in machine shops and manufacturing plants.
3. 5C chuck: 5C chuck is commonly used in lathe and grinder operations. Known for their accuracy and repeatability, they are ideal for holding round, hexagonal and square workpieces. The 5C chuck is also able to accommodate a variety of workpiece sizes, adding to its versatility.
4. Fixed-length chucks: These chucks are designed to provide a fixed, non-flexible clamping on a workpiece or tool. They are typically used in applications where absolute rigidity and repeatability are critical, such as high-precision turning and grinding operations.

Part 3

Application of chuck
Collets are widely used in a variety of machining applications across a variety of industries. In milling operations, collets are used to hold end mills, drills and reamers, providing secure and concentric clamping to ensure accurate, efficient material removal. In turning operations, chucks are used to hold round, hexagonal or square workpieces, allowing precise machining of external and internal features. Additionally, chucks are crucial in grinding operations as they are used to secure the grinding wheel and workpiece with exceptional precision and stability.
The versatility of collets also extends to non-traditional machining processes such as electrical discharge machining (EDM) and laser cutting, where they are used to hold electrodes, nozzles and other specialized tools. In addition, collets play a vital role in tool change systems, such as automatic tool changers (ATC) in CNC machining centers, where they enable fast and reliable tool changes during machining operations.
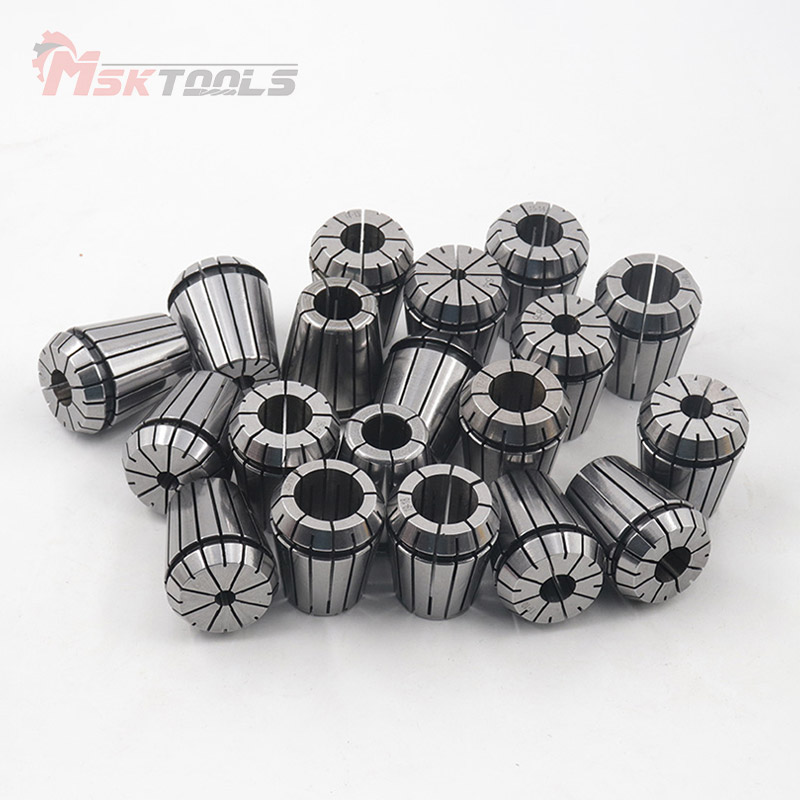
actors to consider when choosing a chuck
When selecting a chuck for a specific machining application, several factors must be considered to ensure optimal performance and efficiency. These factors include the type of machining operation, the geometry of the workpiece or tool, the material being machined, the accuracy required, and the machine tool spindle interface.
The type of machining operation, whether milling, turning, grinding or drilling, will determine the specific collet type and size required. Different chuck types are designed to perform well in specific machining processes, and choosing the right chuck is critical to achieving the desired results.
The geometry of the workpiece or tool is another key consideration. For example, holding a round workpiece requires a different chuck configuration than holding a hexagonal or square workpiece. Likewise, the diameter and length of the cutting tool or workpiece will determine the appropriate chuck size and capacity.
The material being processed also affects chuck selection. Machining hard materials such as titanium or hardened steel may require a chuck with higher clamping force and superior rigidity to withstand cutting forces and maintain dimensional accuracy.
Additionally, the level of accuracy and repeatability required during machining will determine the accuracy and runout specifications of the chuck. High-precision applications require chucks with minimal runout and excellent concentricity to achieve the required part tolerances and surface finish.
Finally, the machine spindle interface is a key factor in chuck selection. The chuck must be compatible with the machine tool spindle interface to ensure proper fit and performance. Common spindle interfaces include CAT, BT, HSK and R8, etc. Choosing the correct collet interface is crucial for seamless integration with machine tools.
In short, the chuck is an indispensable workpiece holding device in precision machining, providing a reliable and versatile solution for accurately and stably fixing cutting tools and workpieces. Their ability to adapt to a variety of tool and workpiece geometries, as well as their strong clamping force and excellent concentricity, make them an essential component in a variety of machining operations. By understanding the different types of collets, their applications, and the factors involved in selection, manufacturers can optimize their machining processes and achieve superior part quality. As technology continues to advance, the development of innovative chuck designs will further enhance precision machining capabilities, drive the development of manufacturing processes, and push the boundaries of what is achievable in the machining field.
Post time: Mar-21-2024